
Use the Eastwood MIG 250 for professional-quality work.

The Eastwood Elite MP200i offers similar power in a multi-process unit. You can order the portable MIG 180 with a spool gun for welding aluminum and can use it for flux-core welding. The Eastwood MIG 180 lets you get a little more serious about metal fabrication and can weld up to 5/16” thick steel using a 240V current, or 3/16” on 120V current since it is a dual-voltage machine. If you want to try other techniques, it’s also offered as a multi-process welder that can do MIG, TIG and stick welding. The MIG 140 is an updated IGBT inverter welder that weighs less than 25 pounds for portability and definitely steps up the performance and features. The MIG 90, which a great welder to try MIG welding, can be used on steel up to 1/8” thick with standard 120V household current. The Eastwood MIG 90 and MIG 140 are great introductory welders for mild and stainless steel. For this guide, we primarily focus on Eastwood welder options however, many similar welders are available from Lincoln Electric and other brands. Our buyer’s guide will help you select the best welder for auto body repairs and custom fabrication. Once you’ve decided on this process, though, you still need to choose the correct welder to fit your needs. Add in the lower machine cost, and MIG auto welding is a clear choice especially among less skilled welders. Metal Inert Gas (MIG) welding is the easiest method to learn and produces great welds fast.
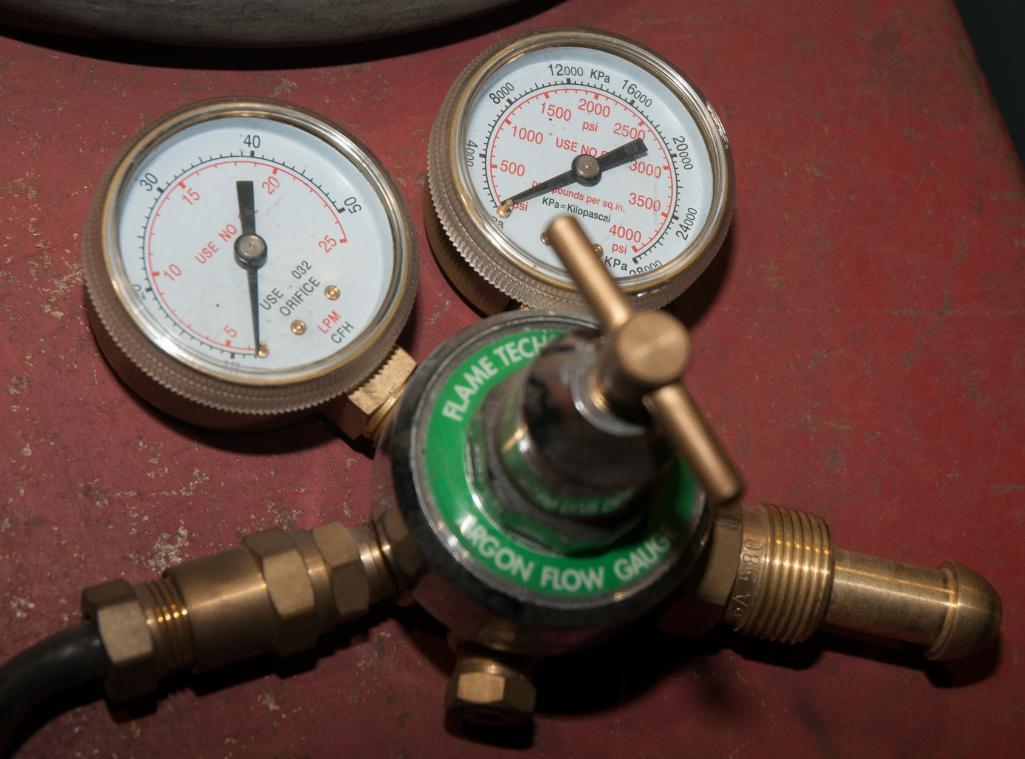
Many DIY metal fabricators new and old choose MIG welders for their autobody work. Headlights - Taillights - Accessories - More.I tried an Esab last year and before we could even fill out the demo papers, it quit, so the guy took it back. All in all.the Snap On always took up the slack when the others were down for repair. Not so good on the cost the most and was broke down the most.probably $3,500 in repairs over the years. The Hobart came in second as far as down time and if I had to guess, maybe $2,000 in repairs over the years, but a lot of down time. They all used about one roll of 035 wire in about three weeks. The Miller needs an $800 circut board (for the second time), and the Hobart is just fried. All three were bought within the same year and as of now.the only one still welding is the Snap On.
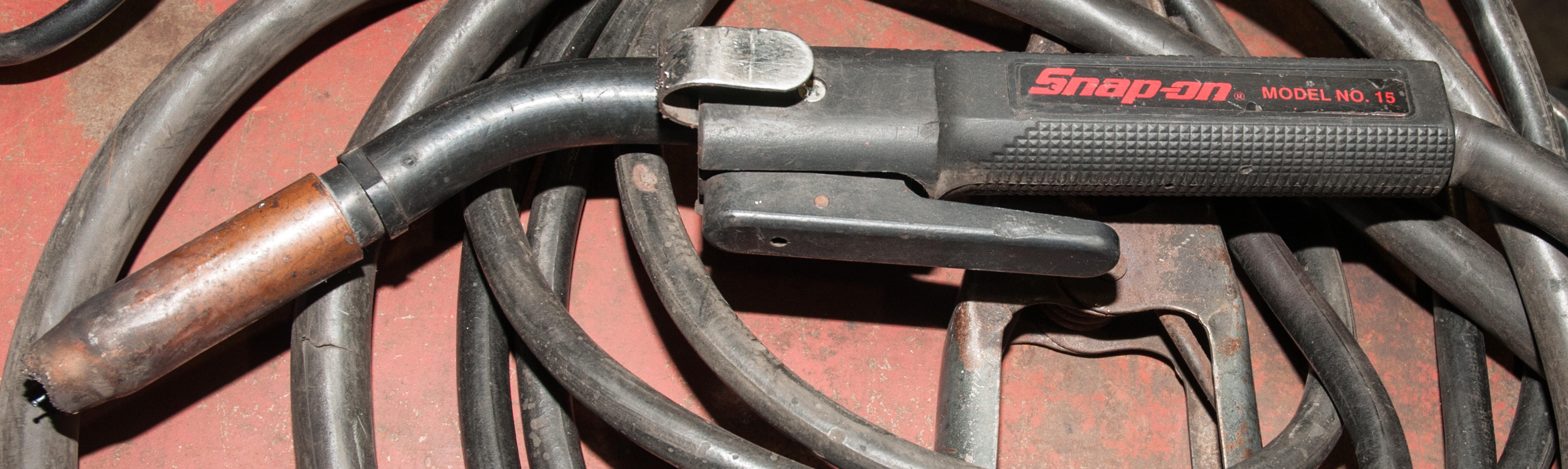
For the last 24 years it has worked side by side with a Hobart and a Miller. If I ever need anything, I get it from them.however, since I have owned it, it hasn't cost me more than $300 other than tips and a few liners. Like somebody else posted, it was made by CK Systematics out of PA.

My Snap On YA212A has out performed all the rest.
